HIPPSC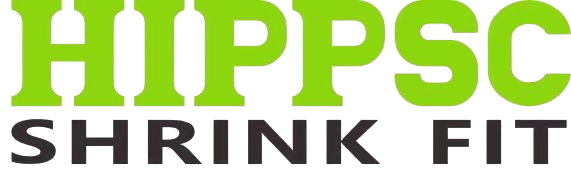
Opening soon
Our site is currently undergoing maintenance. Once complete, it will be accessible at www.hippsc.com. We appreciate your patience. If you have any questions or inquiries at the meantime, please contact kaisen@hippsc.com.
Store access
Enter password below to access the store
This shop is powered by
Store owner?
Login